What is CD stud welding? (Capacitor Discharge StudWelding)
CD Studwelding is where capacitors are used to quickly discharge electrical energy through a threaded or unthreaded weld stud. The electrical energy liquifies the pip of the stud. Simultaneously, spring pressure in the hand tool forces the stud down into the molten pool, forming a weld that is stronger than the parent material. Stud welding is only possible onto metal sheet because of the earth-return process and materials should be matched. i.e. A stainless steel weld stud should be welded to stainless steel sheet metal.
CD stud welding explained in greater detail
How Capacitor Discharge StudWelding fits into the Larger Picture of Welding Methods
Within the fastener world, there is many types of ways to weld metal together. Stud welding is one way to weld materials together. You may find CD is often shortened version of Capacitor Discharge. This is a term used in stud welding to refer to the type of conversion which takes place when using a one hundred and ten volt outlet. Studfast Stud welding has been supporting customers to make efficient and cost effective production solutions for over 30 years. We are based in Northamptonshire and provide our customers with a next day service for all their CD studwelding needs. Stud welding is a fast, reliable and accurate method of attaching a metal fastener to a metal part using an electric arc. Stud welding uses direct current electricity to create an arc between a fastener or stud and the parent material. The parent material or work piece can vary from thin sheet to thick plate. The arc melts the end of the stud and creates a molten pool in the parent material. The weld is completed when the stud is forged into the molten pool under pressure. Usually studs are externally threaded, plain pins (unthreaded) or internally threaded tapped bosses (pads). The equipment required depends on the diameter of the stud to be attached, the condition and thickness of the parent material and the type of material. Typical materials are mild steel, stainless steel, aluminium alloy, pure aluminium and lead free brass. The stud is held in a handtool or welding head which is used to initiate the weld and apply the forging pressure. The handtool and the parent material are connected to a power source (the controller). Stud welding can be used to weld studs from M2.5 to M24.
There are three types of stud welding;
- Drawn Arc (DA),
- Short Cycle (SC)
- Capacitor Discharge (CD).
DA is used for larger diameters whereas SC and CD are used for smaller diameters. The weld duration varies from a few milliseconds for Capacitor Discharge to more than a second for large diameter DA. For DA and SC three phase mains power is transformed and rectified, for CD single phase power is used to store energy in capacitors. DA equipment is larger and less portable than SC equipment. The lightest and most portable equipment is CD. The DA process requires the use of a ceramic ferrule (arc shield), to contain and shape the weld fillet, this is not reusable. Weld spatter is evident with the SC process and this can be minimised using a shrouding gas. Capacitor Discharge is by far the cleanest process with only a small witness of molten metal visible around the flange. The DA weld zone extends into the parent material to a depth of one third of the stud diameter, so plate thickness will determine where it can be used in order to avoid burn through. The SC weld zone enable sheets as thin as 1.5mm to be used whereas Capacitor Discharge can be used on sheets as thin as 0.7mm.
The three types of studwelding are used in different circumstances.
The DA process is the most tolerant of surface imperfections. As long as a pilot arc can be established then rust, mill scale, oil and dirt will not prevent a weld.
Drawn Arc studs have a fluxed weld end and a length allowance for burn off. A good weld is represented by an even fillet and the correct length reduction of the stud. The SC process is also tolerant of surface imperfections and does not require a fluxed stud nor a ferrule.
The CD stud welding process is ideal for thin gauge sheet where reverse marking can be minimised or completely eliminated. For CD the sheet surface should be clean and flat and the weld stud must have a precise pip and cone angle on the weld end. CD studs and CD equipment are lowest in cost and the process is the fastest. Handheld Capacitor Discharge Machines can weld up to 6 studs per minute and automation can increase this to over 20 studs per minute. CD is easy to jig as it does not require ferrules nor shrouding gas and consequently is the most accurate process. The short duration pulse of energy in CD welding imparts local heating only to the weld area thus avoiding heat distortion. Studfast Studwelding supply the full range of all equipment, studs and accessories required to get your started and ensure you do not let your customer down or production coming to a stop.
The benefits of CD stud welding (Capacitor Discharge StudWelding) are:
- The welds are clean and require no finishing.
- The molten metal of a stud weld creates complete fusion across the whole diameter area of the stud which makes the joint stronger than either the stud or the parent material.
A destruction test demonstrates that either a slug of the parent material is pulled out (on thinner gauge sheet) or the stud breaks in the heat affected zone above the weld.
Reliable, repeatable stud welds are achieved under consistent conditions of applied power and weld time.
How Does Stud Welding Work?
The three methods of stud welding are; Short Cycle Stud Welding and Drawn Arc Stud Welding, which both maintain an electrical arc between the sheet metal workpiece or 'job' and the stud. Heat energy from this arc liquifies the metal on both the stud and the job before they are brought together after around half a second depending on the diameter of the stud. The third method is Capacitor Discharge Stud Welding whereby a bank of capacitors instantly discharges, liquifying a small pip on the stud, that remains in contact with the job, in under ten milliseconds of weld duration.
Each method has its advantages and disadvantages. There is a use case that best suits each of the three processes. In total and in order of weld time, going from the shortest weld to the longest process duration, the three methods of studwelding are;
- Capacitor Discharge Studwelding. Also known as CD Studwelding and identified by its seemingly flat profile flanged studs (actually a 2-3 degrees conical incline) and must feature a protruding "pip".
- Short Cycle Studwelding. Also known as SC Studwelding and identified by the studs having a less conical profile than DA, similar to CD studs but with no "pip".
- Drawn Arc Studwelding. Also known as CD Studwelding and identified by its conical tipped studs tipped with "flux".
Studwelding Method | Description of Welding Process | Use Cases including advantages and disadvantages |
---|---|---|
Drawn Arc Studwelding | The stud is lowered to the job and a pilot arc is formed. The stud is then drawn back and the full weld energy is released. This process features longer weld durations up to a second or more at the larger diameters of stud | The Drawn Arc Weld Process requires a ceramic ferrule to be positioned around the stud. This ferrule contains the weld energy and produces a wonderful fillet profile, but it must be destroyed after the weld and adds operator time and mess to the process |
Short Cycle Studwelding | This process is similar to Drawn Arc and can use the same equipment, but with smaller diameters and shorter weld times. No ferrule is required. | The Short Cycle weld process offers deeper penetration into the parent material and is more forgiving of surface imperfections however more weld spatter in experienced. |
Capacitor Discharge Studwelding | A bank of capacitors are charged up. When the trigger in the hand tool is depressed, all capacitors discharge liquifying the pip of a CD weld stud | High quality studs with absolutely consistent pip lengths must be used for consistent results. However the equipment can be powered from single phase (domestic mains electricity) |
Why choose Studfast Stud welding?
Our extensive catalogue of CD weld studs has a fully stocked ranges of aluminium alloy, pure aluminium , stainless steel 316 (A4) and stainless steel 304 (A2), mild steel and lead free brass in many different sizes and diameters. We can offer CD weld studs from Metric threaded and unthreaded 2.5 diameter and 4 milli meter in length up to metric threaded and unthreaded 10 in diameter and 60 milli meter in length, along with all the variations in between.
We are also able to offer larger sizes if your process requires drawn arc, should you require this process instead of capacitor discharge.
As well as the CD Studs you will require we offer equipment which will get you started, you will require a CD Machine which is dependent on the size of stud you are welding. Our recommendation usually is CDM8 which will weld CD studs from 2mm up to diameter 10mm if you are welding mild steel, stainless steel, aluminium and brass. Watch this video to see what is included in a CDM8 and how to get started immediately, https://www.studfast-studwelding.com/weld-stud-clinic/what-is-included-in-a-cdm8-machine/
CD welding is ideal for thin parent material which are flat and clean. Once you CD weld on on the parent material the weld will be clean, neat and strong. You can watch this video to see how to test your weld strength, https://www.studfast-studwelding.com/weld-stud-clinic/how-to-use-a-bending-bar/
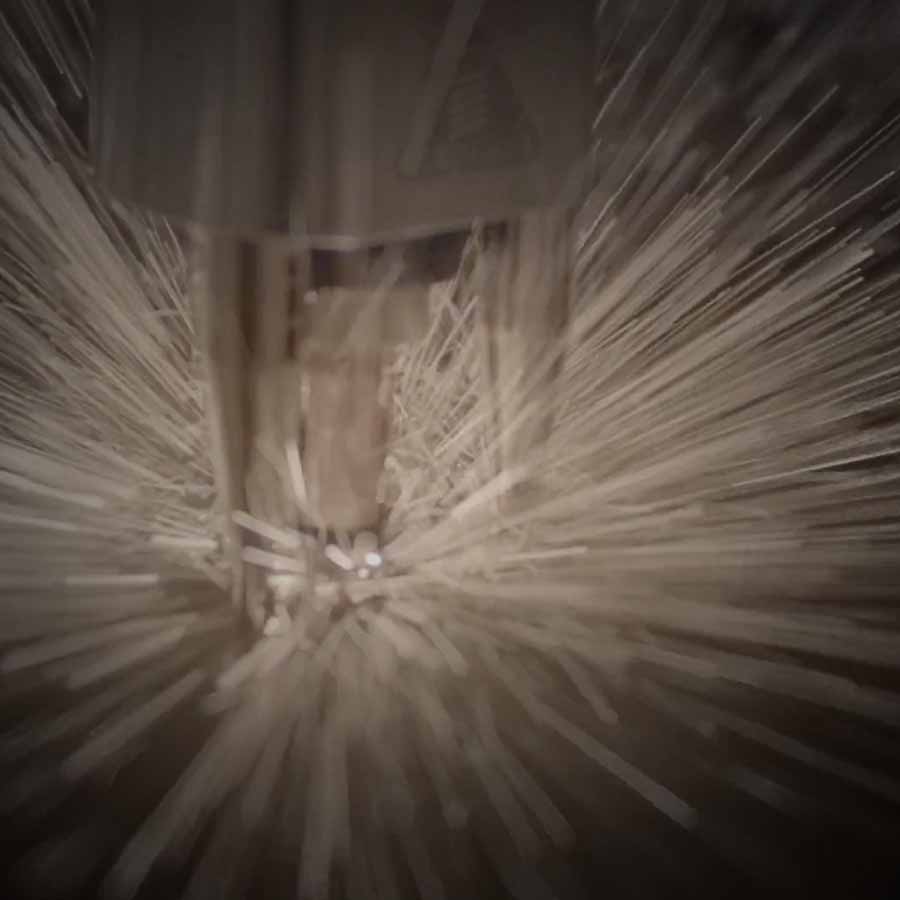
Conclusions on the CD Stud Welding Process using the Capacitor Discharge weld method
CD studs and CD equipment are lowest in cost and the process is the fastest. The Capacitor Discharge stud welding process is ideal for thin gauge sheet where reverse marking can be minimised or completely eliminated. For CD the sheet surface should be clean and flat and the weld stud must have a precise pip and cone angle on the weld end. CD is easy to jig as it does not require ferrules nor shrouding gas and consequently is the most accurate process.
The CD stud welding process is ideal for thin gauge sheet where reverse marking can be minimised or completely eliminated. For CD the sheet surface should be clean and flat and the weld stud must have a precise pip and cone angle on the weld end. CD studs and CD equipment are lowest in cost and the process is the fastest. Handheld Capacitor Discharge Machines can weld up to 6 studs per minute and automation can increase this to over 20 studs per minute. CD is easy to jig as it does not require ferrules nor shrouding gas and consequently is the most accurate process. The short duration pulse of energy in CD welding imparts local heating only to the weld area thus avoiding heat distortion. Studfast Studwelding supply the full range of all equipment, studs and accessories required to get your started and ensure you do not let your customer down or production coming to a stop.